Mandi: A research team from the IIT Mandi, led by Dr. Venkata Krishnan, in collaboration with researchers from Indian Institute of Technology Ropar, is working towards the development of environmentally safe and cost-efficient catalysts that enable industrial chemical reactions.
A catalyst is a substance that can be added to a reaction to increase the reaction rate without getting consumed in the process. The team has recently developed a heterogeneous catalyst based on easily available carbon, for hydrogenation – a class of reactions extensively used in the chemical industry.
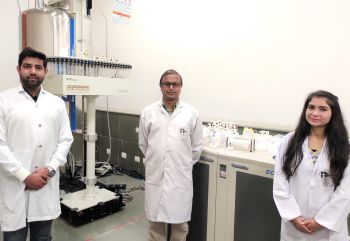
“We cannot overestimate the practical importance of catalysis”, says Dr. Venkata Krishnan, “almost all synthetic products we use in civilised life now relies on industrial preparations, which in turn make use of catalysts.” Catalysts hasten or enable otherwise difficult reactions and help in increasing the yield or rate of formation of the needed products. With increasing concerns about the environmental effects of industrial chemical reactions, there is a heightened need to develop green catalysts – catalysts that do not add significantly to the environmental pollution issues that are usually associated with industrial processes.
Hydrogenation reactions are commonly used to produce compounds such as aromatic alcohols that are extensively used in perfumes, pharmaceutical products, agrochemicals, and fine chemicals. Traditional hydrogenation methods involve the reaction between hydrogen gas and various precursors such as acids, aldehydes and ketones, collectively called carbonyl compounds. More recently, to avoid the exposure and cost issues associated with hydrogen, hydrogenation reactions make use of a safe hydrogen donor chemical.
“This is where catalysts come in”, explains Dr. Krishnan. Hydrogenation catalysts are specialised chemicals that can assist the transfer of hydrogen from cheaper and non-dangerous hydrogen donors to the substrate to be converted to the product of interest. The catalysts that are now used for hydrogenation reactions involve precious metals such as rhodium, iridium, platinum and ruthenium, which naturally add to the cost of the synthesis method, in addition to having environmental issues. Besides, the recovery of these metal catalysts is difficult.
Recently, simple, specialised carbon-based materials have been recognised world-over as easily available, cheaper alternatives to precious metal-based catalysts for a variety of reactions. Such carbon-based materials exhibit significantly high stability and eco-friendly performance. Of many carbon-based materials that are being explored for catalysis, the IIT Mandi team has chosen graphitic carbon nitride (GCN) as a metal-free catalyst for the chosen reaction due to its interesting chemical and physical properties.
“We synthesised heterogeneous catalysts by the chemical oxidation of graphitic carbon nitride (GCN) nanosheets, which results in the generation of water-loving (hydrophilic) carboxyl, hydroxyl and ketonic groups over the GCN surface”, explains Dr. Krishnan. These hydrophilic groups are the active reaction sites for the hydrogenation process. Nanosheets are tiny sheets of the material, a hundred thousand times thinner than a single human hair; at such scales, the surface area on which the reaction can occur is large. In addition to the nanodimension, the functional groups on the surface of the oxidised nanosheets were found to be excellent sites for the hydrogen transfer reactions.
The team investigated a wide range of precursors for the hydrogen transfer reactions using 2-propanol both as a hydrogen donor and a solvent. The nanosheets resulted in high yields and high turnover numbers demonstrating the versatile catalytic potential of the as-synthesised catalyst.
In addition to showing good catalytic prowess of their catalyst in hydrogenation reactions, the team also optimised the reaction parameters and calculated green metric parameters. “An added advantage of our catalyst is that it could be easily recovered and reused for several runs without any loss in catalytic activity”. This property adds to the cost-efficiency and environmental benefits of the reaction. The developed protocol provides a greener, safer and cost-effective approach for large scale applications in the production of the industrially relevant products.